Mastering the Art of Cantilever Construction: A Comprehensive Guide to Project Management
Understanding Cantilever Construction:
Before we delve into project management specifics, it's crucial to grasp the concept of cantilever construction. A cantilever is a structural element that projects horizontally and is supported on only one end. This construction method allows for the creation of overhanging structures, such as balconies, bridges, and even entire buildings, showcasing the architectural prowess of engineers.This is a subtitle for your new post
Key Considerations in Cantilever Construction Project Management:
Feasibility Study:
Begin with a thorough feasibility study to assess the site conditions, soil stability, and environmental factors that may impact the cantilever construction project.
Evaluate the economic viability and potential risks associated with the chosen cantilever design.
Design Phase:
Collaborate closely with architects and structural engineers to develop a detailed and precise cantilever design.
Ensure that the design complies with local building codes and regulations.
Risk Management:
Identify potential risks, such as structural instability, material limitations, or adverse weather conditions.
Develop a comprehensive risk mitigation plan to address and minimize these challenges.
Material Selection:
Choose materials with the right balance of strength, durability, and weight to support the cantilever structure.
Collaborate with suppliers to ensure a reliable and timely source of materials.
Budgeting and Cost Control:
Establish a realistic budget that accounts for all project phases, including design, construction, and post-construction.
Implement stringent cost control measures to avoid budget overruns.
Timeline Planning:
Develop a detailed project timeline, considering the critical path for cantilever construction.
Anticipate potential delays and build buffers into the schedule to accommodate unforeseen challenges.
Communication and Collaboration:
Foster clear communication and collaboration among all stakeholders, including architects, engineers, contractors, and regulatory authorities.
Regularly update stakeholders on project progress, challenges, and milestones.
Quality Assurance:
Implement rigorous quality control measures throughout the construction process to ensure that the cantilever structure meets design specifications and safety standards.
Conclusion:
Successfully managing a cantilever construction project requires a combination of technical expertise, strategic planning, and effective communication. By carefully addressing the key considerations outlined in this guide, project managers can navigate the complexities of cantilever construction, turning architectural dreams into awe-inspiring realities. As the construction industry continues to evolve, mastering the art of cantilever construction becomes not only a testament to engineering prowess but also a showcase of innovation and bold design.
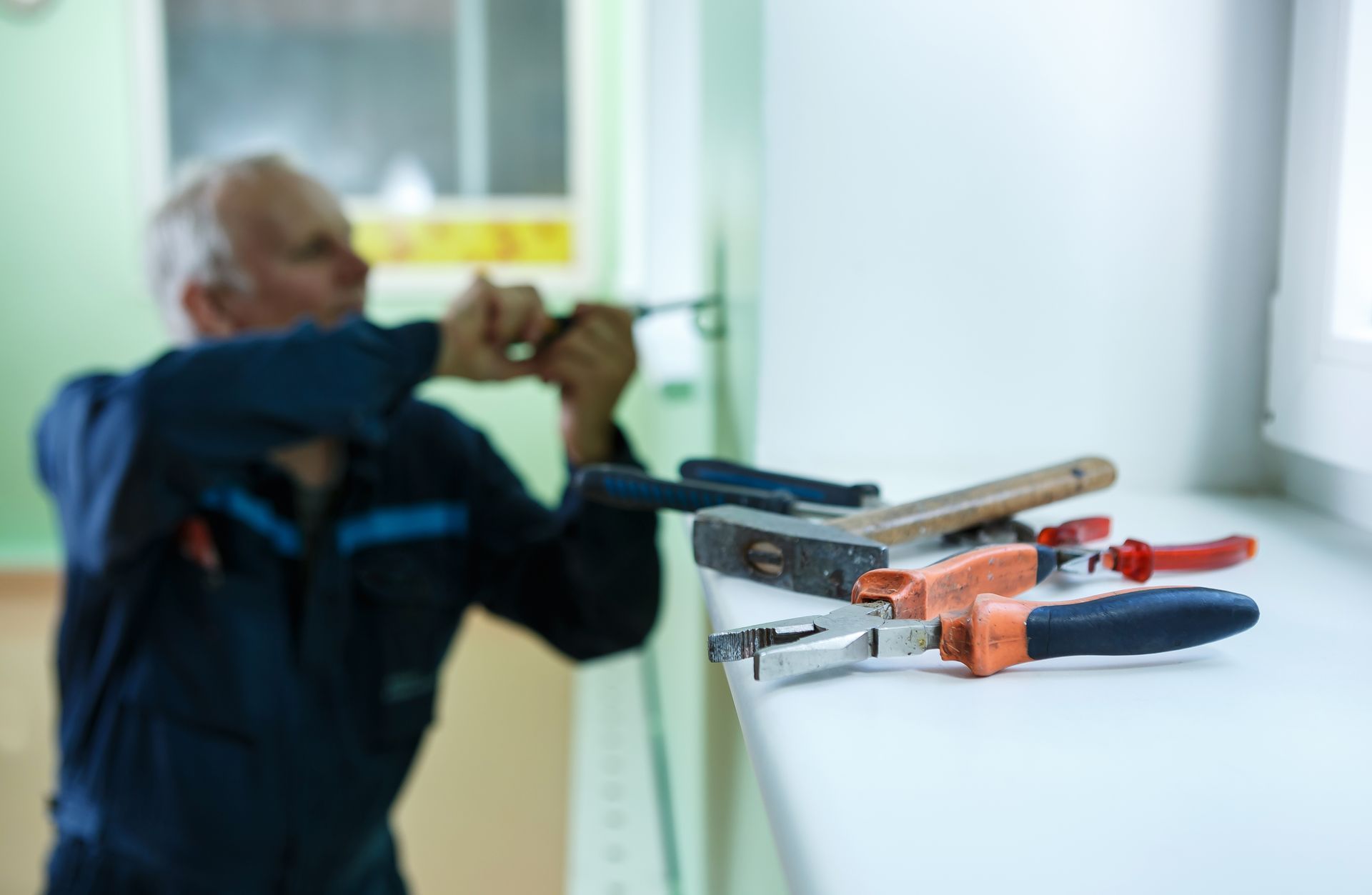
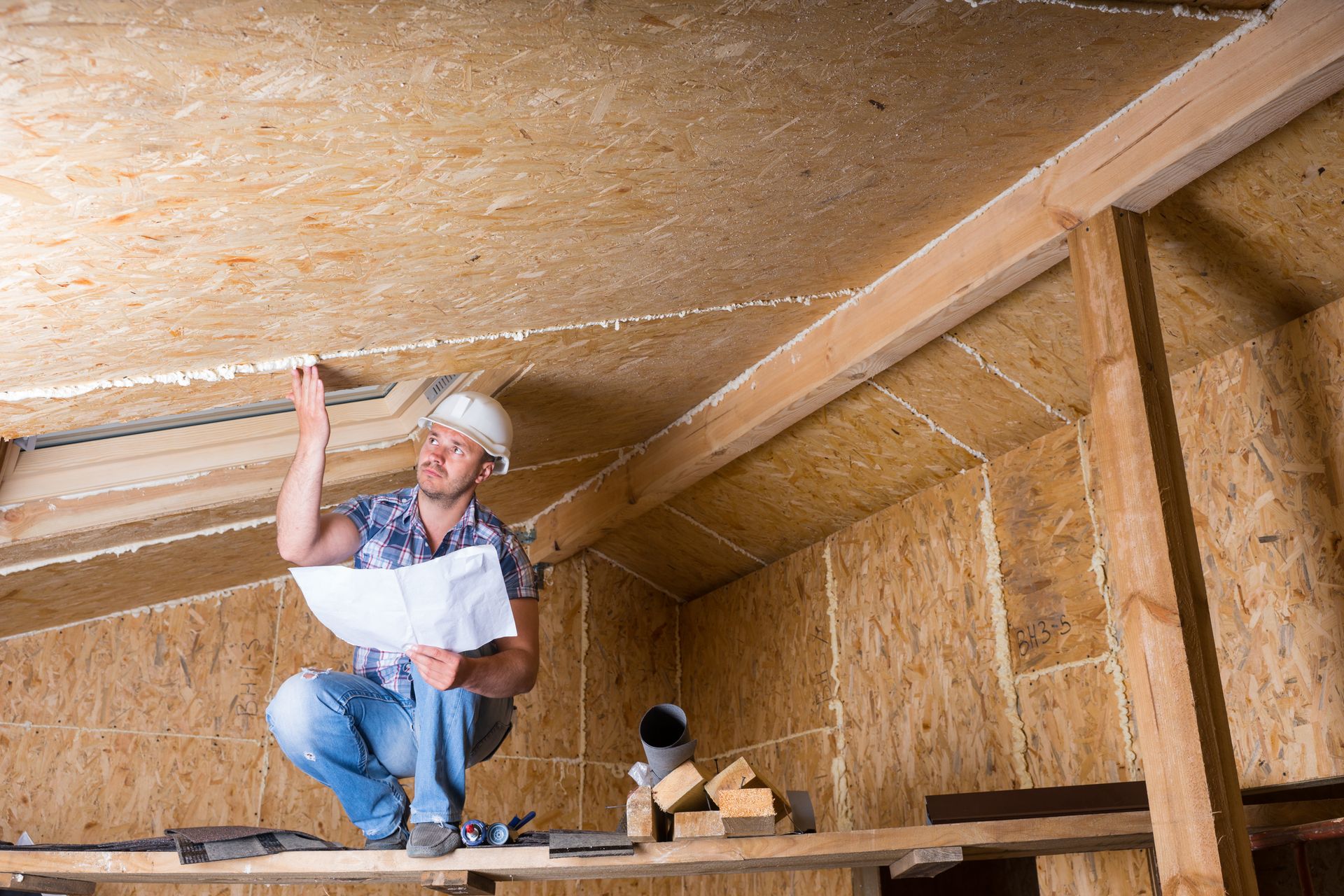
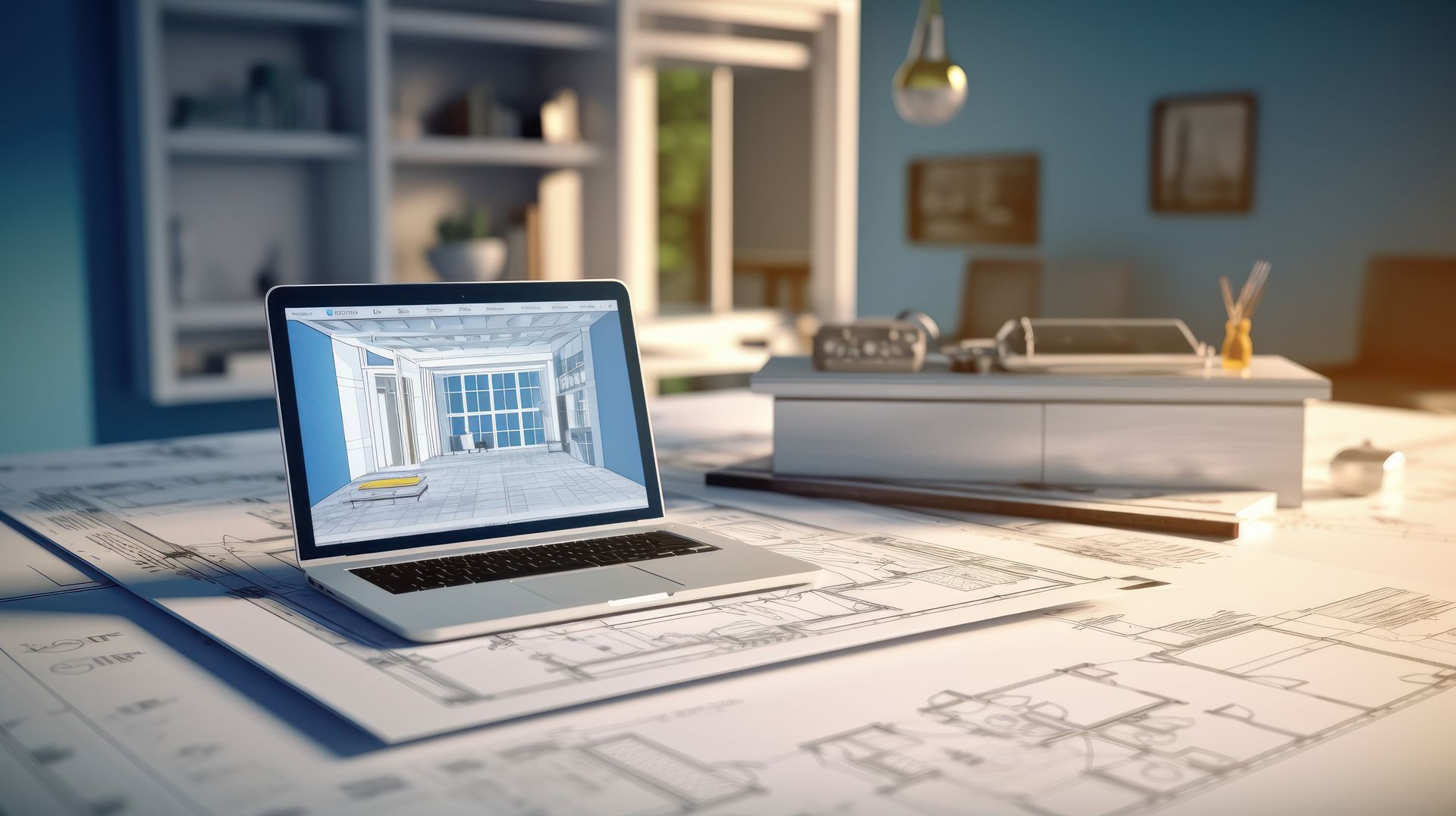